Not every contract manufacturer has the flexibility and capability of quickly switching production between myriad parts, especially in aerospace and medical manufacturing. But that’s exactly the position FPD Co. is in, according to Jeff Speicher, senior vice president and general manager, who attributes such capabilities to Grob Systems Inc.’s automated five-axis machining.
Established in 1980, FPD is an ISO 9001/ AS9100 certified aerospace titanium component and assembly manufacturer. The highly complex components and assemblies produced at its 80,000-sq-ft (7,400-sq-m) facility in McMurray, Pa., support aerospace OEMs and their suppliers. Anodized Aluminium
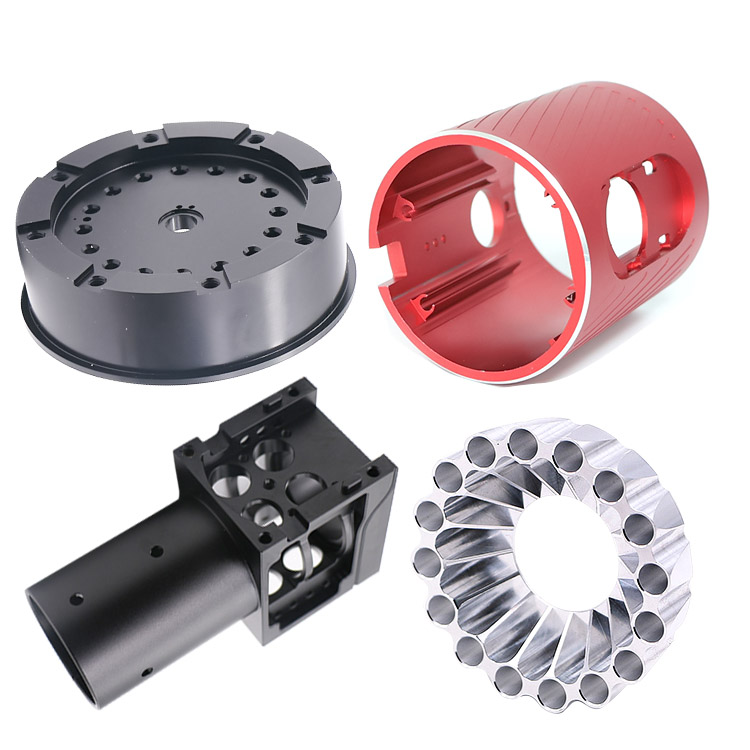
Titanium is in FPD’s DNA. In the 1960s, FPD’s parent company, Dynamet Inc., converted titanium ingot into bar, wire and shapes. Early on, FPD purchased a forging press and eventually began machining serial titanium medical parts such as hip joints and knee implants. Machining was first done via three-axis technology, followed by four-axis systems in the 1990s. In 1997, Carpenter Technology Corp. acquired Dynamet and FPD was ushered into the world of aerospace processed parts. By 2008 the percentage of aerospace parts exceeded medical parts. Today, aerospace accounts for about 90% of FPD’s work—including a wide range of structural parts for commercial airplanes, business jets, helicopters and defense aircraft.
The vast majority of titanium parts that FPD produces has extremely tight tolerances, finish requirements, and needs to meet stringent aerospace and medical specifications.
Rooted in a mindset of “be the best at whatever you do,” Speicher and his team seek the most advanced production technologies. Key goals are increasing cutting tool life, reducing labor costs and eliminating operations—such as offline deburring—to enable the majority of parts to be produced in a single operation. In 2014, FPD realized that leveraging five-axis machining could unlock the potential to scale as a company and support OEM customers by producing superior parts at a lower cost.
FPD began investigating five-axis machine tools and automation at IMTS 2014. Although all of the company’s 30 CNC machines were automated, Speicher and his team wanted the best five-axis machines and automation capabilities.
This eventually led to a visit to Grob’s booth, which most of the team wasn’t familiar with at the time. “Once we saw a demonstration of a G350, we pretty much knew instantly that we were looking at something very different and special,” Speicher says.
“Grob offers a unique solution that others don’t—they design their machines with automation baked in, whereas others design their machines and implement automation later,” he continues. “We knew this would serve us well because we run 24/7 full lights-out production. Grob offers a premier, well-built, highly engineered solution for this environment.”
Grob builds five-axis machining centers for medical, aerospace and mold-and-die applications. Based in Germany, the family-owned company has its North American headquarters and production facilities in Bluffton, Ohio.
In 2016, FPD acquired its first Grob machine, the G350 Universal Machining Center with a rotary Erowa 48-pallet system. The G350 machine is equipped with a Heidenhain iTNC 530, 16,000-rpm spindle, 117-tool holding capacity and an HSK-A63 tool interface.
Grob’s unique machine layout includes a horizontal spindle position, which permits the longest possible Z-travel path and optimum chip fall, according to the company. The arrangement of three linear axes offers stability by minimizing the distance between the guides and the machining point. The tunnel concept allows the large components to be swiveled and machined within the work area without colliding—even with extremely long tools. Three linear and two rotary axes permit five-sided machining, as well as five-axis simultaneous interpolation, with a swivel range of 230° in the A-axis and 360° in the B-axis.
“There are inherent advantages of horizontal machining centers and FPD Company knows this very well. When FPD was looking to add five-axis capability, the horizontal spindle was a must,” says Mark Schem, technical sales manager at Grob. “By partnering with Grob, they were able to utilize our unique kinematics of a rigid horizontal spindle along with the added benefit of inverting the table upside down for best chip evacuation.”
FPD first implemented the G350 automation system for medical part production. Prior to this, a cobalt chrome casting for a knee implant with a highly polished surface was running on a four-axis machine with a traditional pallet system that required one operator per shift.
“The Grob solution is not only faster, providing cycle time reductions, but the part quality it produces is superior,” Speicher asserts.
The G350 was just the start of FPD’s automation transformation. By 2018, the first of six Grob G550 5-Axis Universal Machining Centers with a 9,000-rpm HSK spindle was installed, which was the start of what became an automated, multi-machine line to produce parts for Boeing and Gulfstream aircraft. The six G550 machines are connected by a shared pallet system and tool magazine.
“The G550 featuring a high-torque HSK-100 spindle was the perfect machine size for FPD. The 630-mm pallet and 900-mm work cylinder complemented the majority of FPD’s part sizes and material. Having the five-axis capability allowed FPD to transfer jobs from their existing four-axis machines to the Grob cell and reduce part operations,” Schem says.
Grob and FPD collaborated to design the line along with supporting software programs that enabled FPD to react to unplanned jobs in a moment’s notice. “In fact, we can change job priorities right from our cell phones,” Speicher says. “Now a tool magazine serves each G550, so two to three machines can run the same part and same program with the same tools ... (and) we are fully capable of running any part at any time on any machine, with a click of a button. The Grob line gives us the freedom and productivity to achieve this, which we didn’t have before.”
The pallet system incorporates a robot to shuttle material and complete parts to and from the operator load station. A second overhead gantry robot transfers cutting tools to each machine from a central tool storage magazine or “tool hive.” The tooling robot also transfers cutting tools between machines as needed during the execution of the machining process. Prior to the automated Grob setup, a separate tool magazine was needed for each four-axis machine, which could add significant operational costs.
“Our four-axis machining centers have tool magazines with a capacity of 300 tools in each machine,” Speicher explains. This means we needed 1,800 tools to fully tool-up the six four-axis machine pallet systems. However, many of the tools were idle, not being used often.”
Since adding five-axis machines to its facility, FPD has realized a 62% cycle time reduction and improved machining accuracy to the nominal part geometry. “By using a common tooling package, along with a tool hive and automation, tools are shared among multiple machines seamlessly,” Speicher says, “and because of this we are seeing a huge advantage in efficiency, quality and cost.”
“Having the six Grob machines together in a turnkey automation line with the pallet system and tool magazine has given FPD the opportunity to competitively bid and win approximately $9 million in additional annual sales, representing a 23% increase in revenue each year,” notes Daniel Gordon, FPD sales and marketing manager. “The direct labor cost of the Grob five-axis systems is 43% lower than our four-axis systems, which makes us even more competitive.”
Key in achieving this kind of success is thorough after-sale service. “When we rolled this system out, Grob was very hands-on with training to ensure that our machine operators, foreman and management were comfortable with the automated line,” Gordon says. “In the beginning we needed some extra attention from a maintenance standpoint and the Grob technicians taught our in-house maintenance team how to perform jobs.”
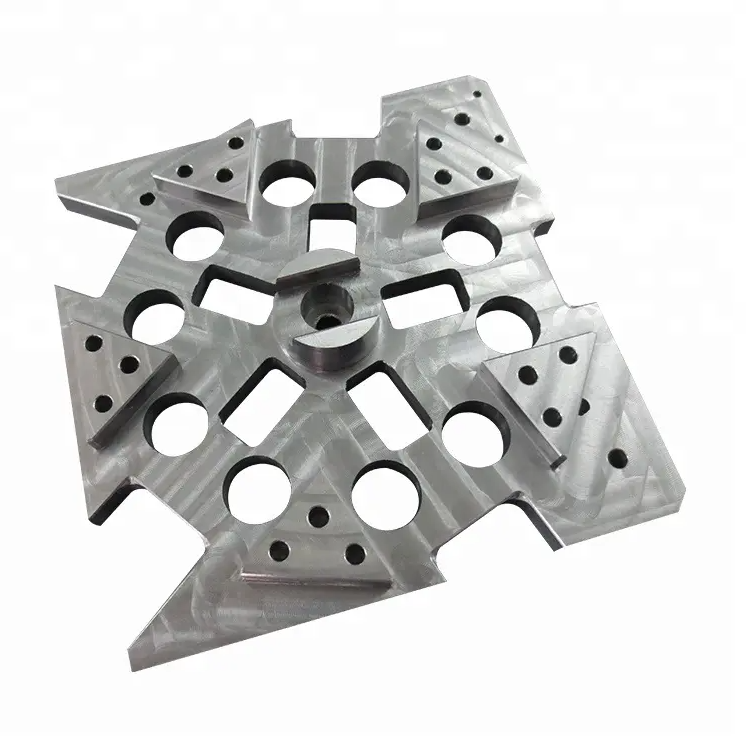
Custom Cnc Milling Parts Not only is 100% of FPD’s machining completed in the Grob system, Speicher says the line constantly gives the team “aha moments” via new opportunities to leverage automation. Grob has been instrumental in FPD’s growth by allowing the shop to machine critical parts at high volumes with extreme efficiency and repeatability, while eliminating many secondary machining operations.