FIGURE 1. An operator grinds with a bonded abrasive.
The grinding and finishing department remains one of the most manual and misunderstood areas of the fab shop floor. A fabricator might scrutinize nesting to optimize material yield, dial in blanking parameters to achieve that perfect laser-cut or punched edge, then scrutinize forming for optimal quality and bend-angle repeatability. After that, parts flow to the grinding and finishing department where, all too often, workers struggle using inappropriate tools and inefficient techniques in an environment that hinders quality and throughput. Fiber Grinding Wheel
.jpg)
How can a fab shop turn things around and boost productivity in what remains the most manual of all metal fabrication processes? It starts with the goal in mind, including the metal that grinders need to remove and the surfaces that finishers need to achieve.
All abrasives remove material, but how and why abrasives are used varies greatly depending on what an operation needs to achieve. Abrasive use in metal fabrication falls into one of three areas: Grinding works well for heavy metal removal, like when grinding down welds (see Figure 1); blending helps blend different areas of the workpiece (see Figure 2), like when blending welds with the base metal; and finishing prepares a surface with a specific scratch pattern.
For the most part, those grinding use bonded abrasives for aggressive and effective material removal, while those blending use coated abrasives, which have similar abrasive grains but with a cloth underneath that helps improve the surface finish. Those who perform finishing draw from a variety of media depending on what they need to accomplish, from coated abrasives to nonwoven and other surface-conditioning materials, as well as cup discs, buffing drums, and polishing pastes designed to create an aesthetically pleasing mirror finish.
Another fundamental involves looking at overall throughput of a grinding and (especially) finishing operation. Throughput isn’t just governed by how quickly an abrasive removes material. Changing abrasive media takes time—a fact that shouldn’t be ignored.
Finishing is all about creating specific scratch patterns on material surfaces. To achieve them, operators might make their way through various steps, progressing gradually through finer and finer grains. This seems logical. After all, as operators step down to a finer abrasive, they replace slightly coarser scratches with slightly finer ones.
Assuming finishers used the proper technique, the finishing process itself—that is, the time the abrasive media contacts the material surface—might be quite efficient. But what about the entire process, including media changeover and cleaning between steps? That time adds up, and the extra steps can complicate the entire operation.
Observing experienced finishers can reveal what’s possible. They might start with an extra-coarse media, one medium-grain product, then one fine-grain product, after which (if the application requires it) they’ll start polishing. They might spend more time with each abrasive product, but they don’t spend as much time changing out their finishing media or cleaning. And it’s not because they’re spending less time cleaning between steps; they just have fewer steps.
How exactly do they accomplish this? Part of it involves learning how to work the finishing media; another part involves forgetting what they learned in the grinding department.
Grinders might work their way up to the finishing department. It’s a natural career path, but those shifting between the two can develop some bad habits. What works in grinding doesn’t necessarily work for finishing. The two processes really are different animals.
Think of grinding wheels as the wheels on a car; in both cases, the edges do most of the work. Grinders approach the work at high RPM and a high angle of attack, allowing them to contact the work at high speed and high pressure. Think of abrasive discs as disc brakes on a car. The majority of the disc surface does some level of work. This requires a flatter angle of attack (see Figure 3).
If you walk into a finishing department and hear tools whining, with the pitch rising and falling, something is likely amiss. Rookie finishing operators might be carrying over what they did for grinding—approaching the work at a high angle of attack with a lot of pressure. Now in the finishing department, they’re digging into the metal with an abrasive product that was not made to dig at all. At the same time, their excess pressure is creating deeper scratches that will require extra steps to remove. Moreover, operators tire quickly as they push their power tools harder than needed, so their work becomes less consistent. By working harder, they’re creating more work for themselves.
Abrasive finishing discs (see Figures 4 and 5) are made to be applied gently (relative to grinding) on the surface to remove coarser scratches and replace them with finer ones. Experienced operators aim to use them at their optimal, not maximum, rated RPM. Those new to finishing might read the “maximum RPM” rating on the label and think that setting will be the fastest way to finish a product—but the opposite is true. A maximum RPM rating shows the fastest an operator can use the product safely; the optimal RPM shows where it can be most effective for many applications.
A 10-amp tool designed to hold media up to 5 in. dia. might grind at 11,000 RPM but perform finishing steps at between 5,000 and 7,000 RPM. That said, the best RPM to use depends on the product being finished and the available amps a power tool has.
Speed also changes with the disc diameter. Abrasives near the disc’s outer circumference will rotate faster (that is, have a greater linear speed) than abrasives near the center, and the change becomes more pronounced the larger the disc is. Abrasive near the edge of a 7-in.-dia. disc turning at 5,000 RPM is moving faster than abrasive near the edge of a 4.5-in. disc. Their rotations per minute are the same; the abrasive on the 7-in. disc just needs to travel around a longer rotation.
This difference is why you’ll often see experienced finishers adjust the pressure they apply ever so slightly as they move into corners, to blend the scratch pattern throughout the workpiece. Specifically, they might lighten their pressure as they move into a corner. In the center of the workpiece, the entire disc applies a scratch pattern, so any difference in abrasive speed pretty much cancels itself out. But in the corner, the situation changes. Only the abrasive near the edge of the disc can reach the corner, so the “average speed” of the abrasive grains doing the work increases. So, the experienced finisher lightens up a bit to compensate.
In general, such pressure adjustments are minute and subtle. In fact, for any process using abrasive media—grinding, blending, or finishing—consistency is paramount. Someone who can maintain optimal pressure throughout is usually the most effective. Again, listening is important. Hear a whine of a power tool that continually gets higher and lower, and there’s a good chance an inexperienced finisher isn’t applying consistent pressure.
Consistency in movement also matters, a lesson learned in many a grinding department that’s produced workpieces with bluing. Bluing occurs from overheating, and to avoid it, a grinder keeps the tool constantly on the move.
Abrasive choice also matters here. Bonded abrasives continually break down, so if an operator moves the wheel consistently and constantly across the work, heat evacuates. Coated abrasives, on the other hand, have only one layer of media coated onto the disc. So, heat generation can be quite intense if the operator doesn’t follow the right pattern of movement to evacuate heat across the part.
Modern coated abrasives, especially sanding discs, have become some of the most misused tools in metal fabrication. Ironically, some of it has to do with just how well modern abrasive media work.
FIGURE 2. An operator uses a coated abrasive for blending.
Ceramic and precision-shaped grains tend to have extremely high metal removal rates their first five minutes of use. Then their effectiveness drops some—not dramatically, but enough so that many operators take time to replace their disc. The truth is that disc likely has an hour or more of useful life before its removal rate drops dramatically and the disc really does need to be replaced.
Replacing media so often drives up abrasive costs. One could make the argument that maintaining that ultrahigh removal rate would be worth all the extra consumable costs, but that argument doesn’t incorporate the effects of tool-change time. This again goes back to looking at the entire finishing cycle. Finishing slightly slower with fewer tool changes wins the race.
No one wins the race if they aren’t given the right tools. This includes being given the right abrasive media and the right power tool. Say someone attempts to place a certain scratch pattern on a workpiece while using a power tool without variable speed control. Or, despite their proper technique, they find they continually need to change to different grit sizes, yet a more versatile flap disc (with aggressive grit on the flaps complemented by a softer backing underneath) might better suit their needs.
Environmental factors also play a role. Media shouldn’t be stored in excessively dry or humid environments. Work should be free of contaminants, especially if an operation processes both stainless and carbon steel. Ideally stainless and carbon should be processed and (especially) stored separately, not just on different tables or racks within the same cell, but in entirely different areas of the plant.
One stainless steel fabricator recently spent time troubleshooting a rusting problem. The operation waited 24 to 48 hours to ensure the stainless was completely passivated, and yet rust still appeared on a portion of the delivered product. The grinding and finishing department was clean and well-organized, complete with filtered air. The finishing department wasn’t the culprit; it had to do with how work-in-process was stored. The stainless being finished had been stored on carbon steel racks after blanking.
Also, don’t forget about the light. Operators need to see what they’re doing. Too often, fab shops don’t realize that parts don’t have the finish everyone expected until those parts sit near the shipping dock, with light streaming in from outside. Why didn’t anyone notice? Blame poor lighting in the finishing department.
The type of light and level of brightness can be factors, but the important consideration is usually where the light comes from—that is, its direction. Ideally, light should come from multiple directions, allowing operators to inspect the final scratch pattern from every angle.
Throughput in grinding and finishing is about paying attention to the details. In this way, the operation is a bit like baking a cake. Miss one ingredient, and the result won’t be as tasty.
To this end, many operations document their grinding and finishing practices by developing recipes. They detail the finishing steps required—not too many, not too few—the time to take at each step, the technique (flat approach angle, pattern of motion, pressure, RPM), the required cleaning between each step (the cleaning solution to use along with a microfiber cloth), the abrasive media, and power tool settings.
Next, combine these recipes with a good kitchen (clean, well-lit shop with the right tools) and a few chefs who never stop learning (training and documentation about proper technique and finishing steps). Mix all these ingredients together in the right way, and quality and overall throughput are sure to improve.
Product Manager for Finishing and Brushing
See More by Antoine Guay
See More by Mykolai Dutkewych
Read more from this issue
Find The FABRICATOR on Facebook
Find The FABRICATOR on Twitter
The FABRICATOR is North America's leading magazine for the metal forming and fabricating industry. The magazine delivers the news, technical articles, and case histories that enable fabricators to do their jobs more efficiently. The FABRICATOR has served the industry since 1970.
Easily access valuable industry resources now with full access to the digital edition of The FABRICATOR.
Easily access valuable industry resources now with full access to the digital edition of The WELDER.
Easily access valuable industry resources now with full access to the digital edition of The Tube & Pipe Journal.
Enjoy full access to the digital edition of STAMPING Journal, which serves the metal stamping market with the latest technology advancements, best practices, and industry news.
Easily access valuable industry resources now with full access to the digital edition of The Fabricator en Español.
How did two Chicago-area brothers go from having zero fabrication background to creating a business designing and building...
© 2023 FMA Communications, Inc. All rights reserved.
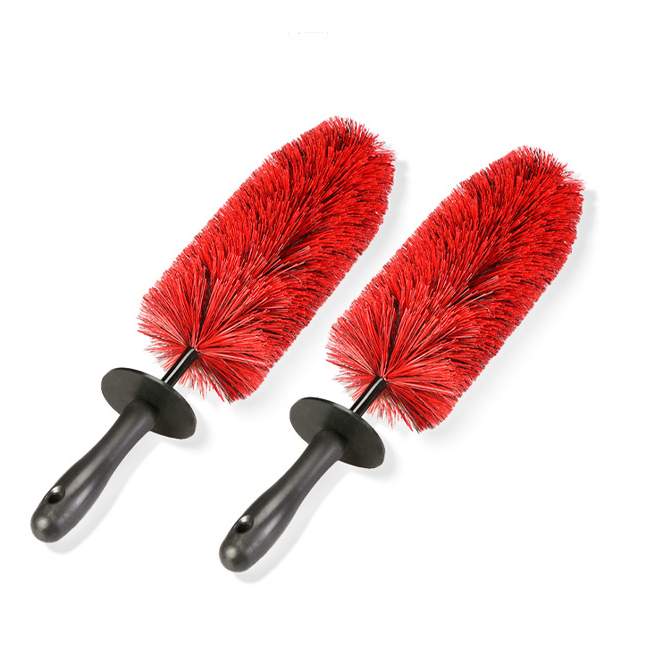
Aluminium Cutting Disc Not yet registered? Sign up